An exploration into making PVT panels suitable for use at sea
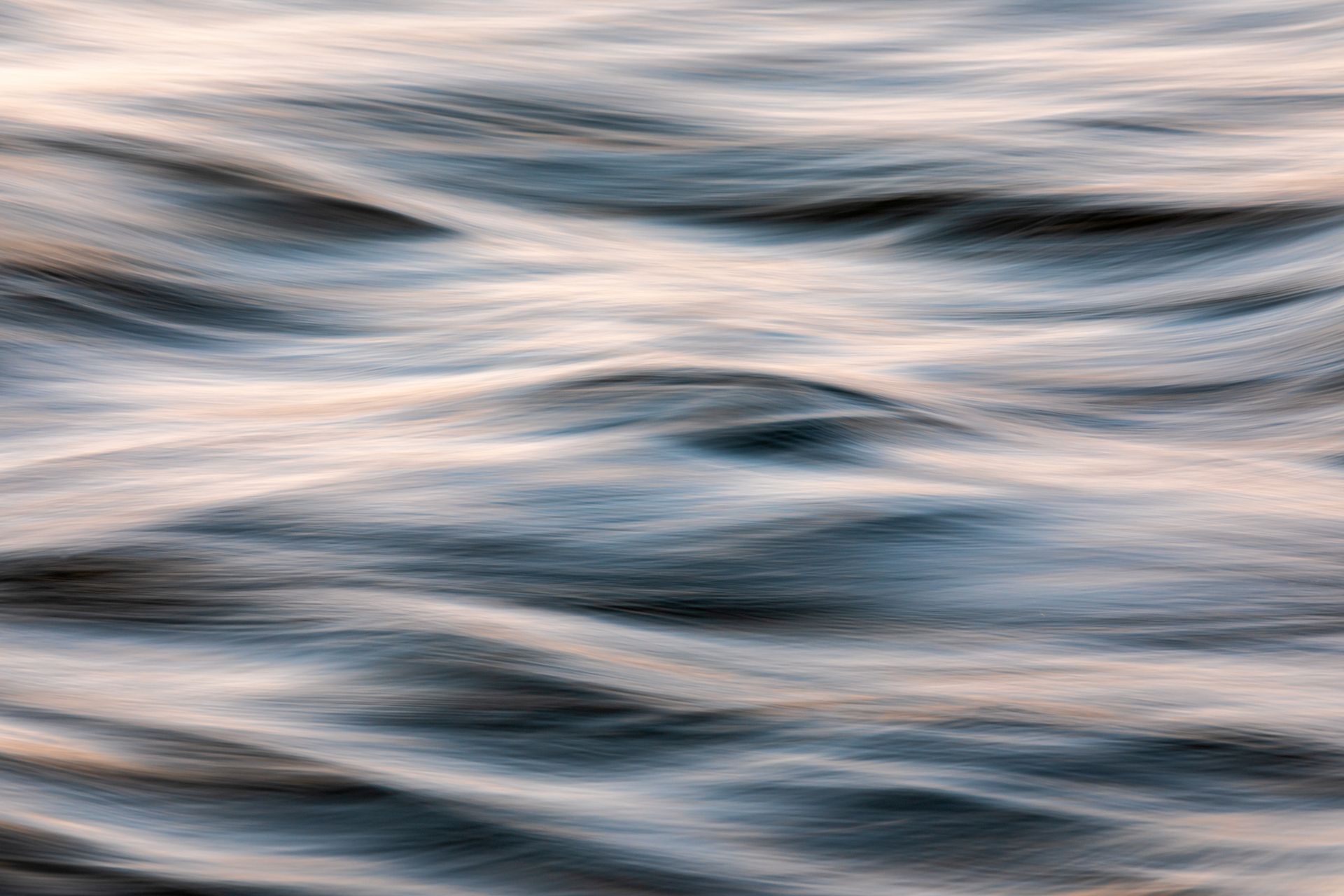
Building a fossil fuel free sailboat is a tough task. You have to balance a range of different factors, ensuring performance and comfort go hand-in-hand, all while managing energy collection and storage in the most efficient way.
When you are out at sea and relying on renewable energy, you have to make do with the power sources available. You can use the water, wind and, importantly, the sun.
Today, we’re going to be exploring the latter. We're follopwing the construction of the sailing boat 'Project Zero' and specifically how it plans to harness solar energy using custom photovoltaic thermal hybrid solar collector (PVT) panels.
To understand this process — and why it’s so vital for the vessel — we spoke with Bob van Someren, an expert who has a PhD in Physics and is the tech lead at Elf Software Development, a company that specialises in the modelling of complex systems. For the development of the sailboat Van Someren helped develop the custom PVT panels. Let’s dive in.
The problem with traditional PVT panels
When you are considering building a sea-faring vessel that needs to generate solar power by itself, you are immediately hit with an issue: space
“You have to match energy usage with what you can generate on that surface area from solar power,” Van Someren says. This is especially pressing when building a consumer boat, as aesthetics have to come into play. Not many of us would want to spend time on something that is completely covered in panels, after all.
Because of the limited space available, you can’t simply generate only thermal or electrical power from the sun — instead, as Van Someren explains, “you need to use the same surface area to generate both electricity and solar heat.”
This comes with its own restrictions though. There’s an inherent tradeoff when generating heat and electricity using the same panels. Specifically, “the warmer the solar panel becomes, the lower its electrical efficiency, but the higher its thermal efficiency.”
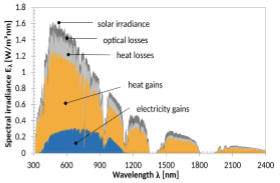
The reverse is also true. If you keep the heat of the panel down to improve electrical efficiency, you’re unable to generate thermal energy that’s functional for the tasks at hand.
Van Someren sums it up: “You want to harvest the heat at a high enough temperature to be useful, but at the lowest possible temperature to have more electrical output.”
Striking the perfect balance
For the PVT panels to operate as efficiently as possible, Van Someren and the project team searched for a middle ground.
“You have to use solar cells that are less sensitive to higher temperatures” because then you can use them in hot environments,” Van Someren says. This could mean their initial efficiency at room temperature is lower than other panels, but they can perform better in the sailboat’s various environments.
“The other choice you have to make is the specific temperature you harvest heat from the panels at,” Van Someren says. For example, if you harvest at 40 degrees Celsius, you can use it to take a shower, but the potential for its long-term use isn’t high. Storing heat often involves an unavoidable drop in temperature, and there are not many useful applications for heat at that level in this situation.
On top of that, it is planned to use an adsorption chiller on the boat, a device that uses hot water to actively cool the vessel. For that machine to operate properly, it requires harvesting heat somewhere between “60 and 75 degrees Celsius.”
What was required is a hybrid panel that’s able to both generate electricity and capture thermal energy efficiently at temperatures of around 70 degrees Celsius.
The problem? A PVT panel like this doesn’t exist.
Is insulation the answer?
The issue — and what Van Someren needed to find an answer for — is all about insulation.
For a PVT panel to work efficiently at generating both solar and thermal energy, it needs to both block and absorb heat.
Let’s begin with the latter: absorbing heat.
“There’s a surface area on the panels that’s black, and that absorbs the energy from the sun,” Van Someren tells me. Part of this is heat — and the sailboat must use as much of this as possible, all while ensuring that it doesn’t dissipate into the environment.
“So what you need to do is to build good thermal insulation around the black areas.” On the bottom of the panel, you can use a relatively standard solution, which involves insulating it with a material similar to styrofoam.
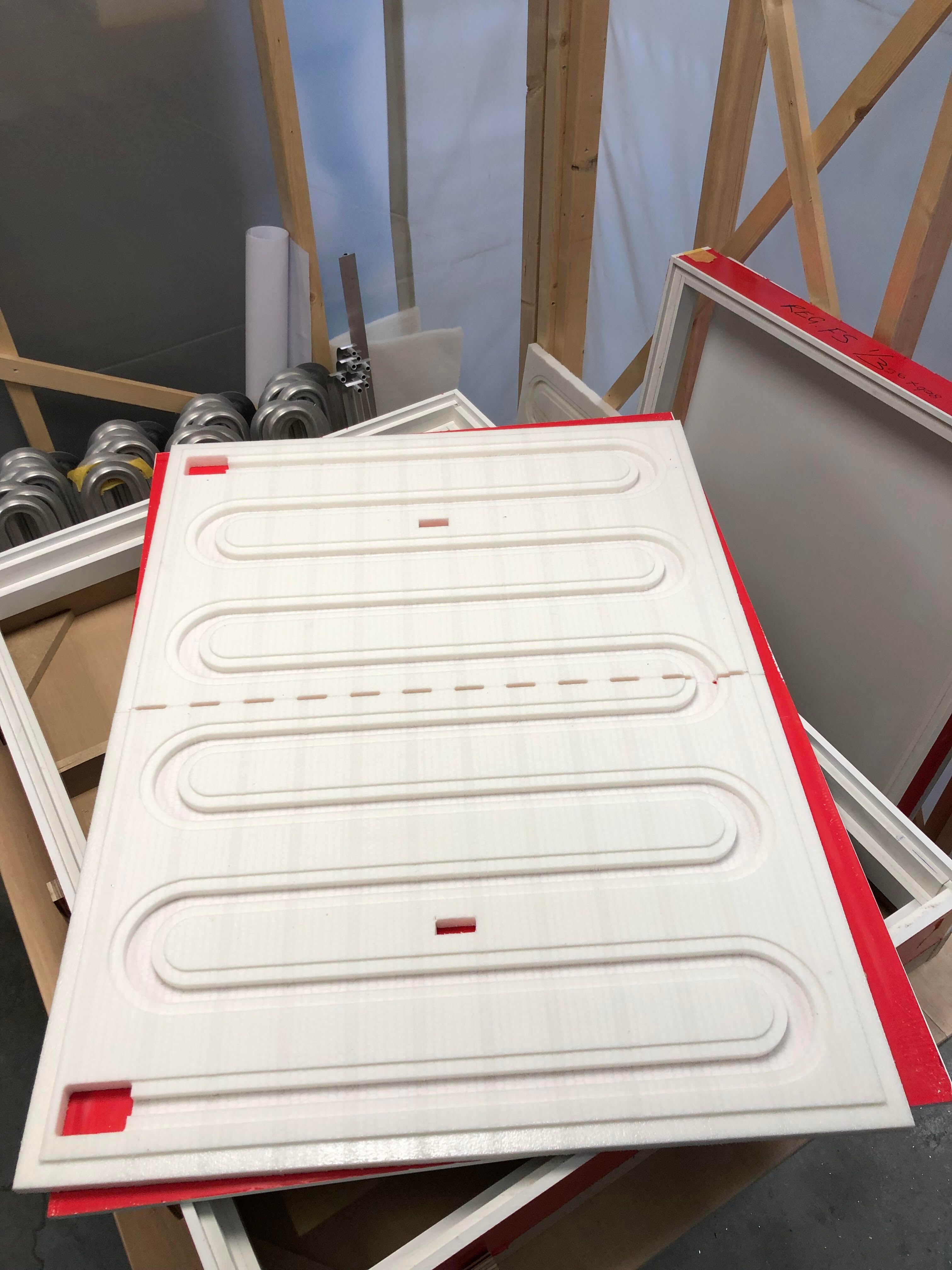
The top, though, proved more difficult.
“The front surface of the PVT panels needs to be transparent — this is to let the sunlight enter — but you also want to block the heat,” Van Someren tells me. This is so electricity can be generated from the sun’s rays, without these elements becoming too hot and reducing their efficiency.
First stabs at finding a successful solution
The original idea was for a filter to sit over the PVT panels, and the team selected a mixture of glycerin and water.
“The reason is that glycerin nicely absorbs the light that the photovoltaic can’t convert,” Van Someren says, as well as the fact the substance is biocompatible, meaning it’s not poisonous and is safe for humans and other lifeforms.
On top of that, “it's very affordable, easy to work with, lowers the freezing point and increases the boiling point, which is also good.”
What the team did was to pump this glycerin mixture between two sheets of glass that sat on top of the PVT panels. This is hugely beneficial, as sunlight comes into contact with the water, heating it up, but as the liquid is being pumped, it moves the heat away, cooling the panel in the process.
Unfortunately, the team bumped into two problems during this step.
The first was due to the space the panels take up. “If you have a low pressure differential over a large surface area,” Van Someren says, “you get a very large force.” This meant the glass plates began to buckle, as the construction wasn’t made to handle those pressures.
Alongside this, the team noticed there were bubbles in the liquid. To flush these out, they increased the pumping speed — and this led to a glass plate blowing up.
“Now, we could have solved that,” he tells me, “and we did actually solve that in a makeshift solution,” but a bigger issue reared its head: fungi.
Life finds a way
After a few days of leaving the system running, they spotted growth in the water.
“Because glycerin is biodegradable,” Van Someren tells me, “it means microorganisms can live off it.” The mixture of nutrients and warm water meant “all kinds of algae and bacteria started to grow.”
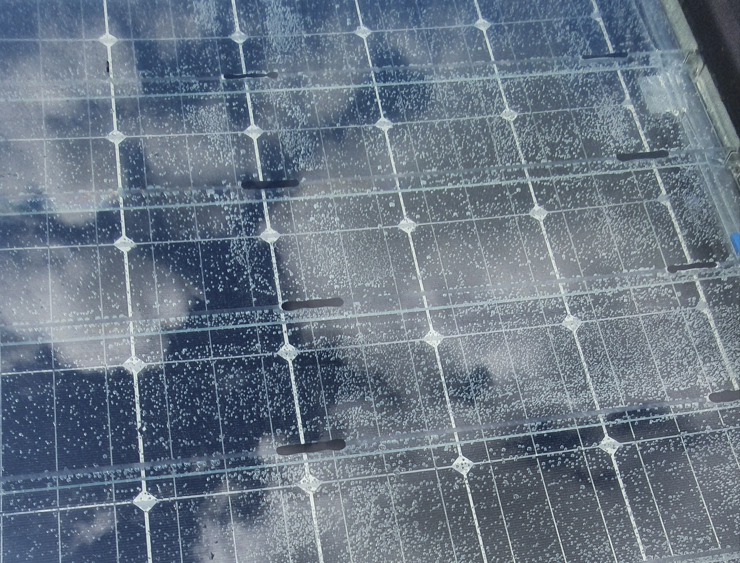
The team’s next step was to fight the biofouling. Immediately, poisoning the water was taken out of the running, so they explored whether they could find a chemical that was safe, but disliked by fungi. This hit a blocker pretty quickly, though.
“We had to abandon that idea because of the time schedule,” he says, explaining the team needed to be pragmatic and work with something that requires less research and development.
The development team pushed forward with a few other ideas. One was putting the entire water system under vacuum, but this didn’t have any impact. The other attempt was using distilled water — a substance containing nothing but water — in an attempt to remove any signs of life.
“We added glycerin … into a container and put it outside in the sun,” Van Someren says, “three days later there were flakes of fungi growing.”
They decided to stop this avenue of inquiry. With more time, it could’ve been possible to overcome, but, in this instance, life won out.
Further attempts at perfecting the panels
The next thing the team tried was the sort of double glazing used in houses, but this was too heavy for the sailboat. After this, the Zero team tried using a technical silicon rubber, specifically a type used for lighting.
This, Van Someren says, performed impressively. “It’s very, very transparent, the surface doesn’t reflect a lot,” and “it resists ultraviolet radiation,” meaning it doesn’t easily turn yellow, which can block the light over time.
It seemed like a perfect solution. And it very nearly was, until the issue of adhesion reared its head.
A sticky situation
While the technical silicon rubber itself is an excellent solution, the team experienced a problem when attaching it to the aluminium of the boat — a material that is vital for the construction of the sailboat.
Van Someren explains that because of the boat heating during the day and cooling during the night, the silicon layer expands and contracts, eventually detaching. Unfortunately, this isn’t a problem they could solve themselves. Instead, it would require huge, industry-level investment to address.
This led the team back to the drawing board.
After further serious deliberation, they settled on a set of glass panes separated by a vacuum they could place over the PV cells. This is like a thinner form of double glazing, around 6-7mm thick, but instead of using a gas between the two panes, it uses a vacuum instead, which delivers both excellent thermal insulation and transparency.
While there are some elements still to improve, such as increasing transparency further, this solution delivered good results for the PVT panels overall.
Van Someren says they use “photovoltaic cells that are relatively insensitive to high temperatures” and “thermal insulation that allows about 60% of the solar energy it collects” to be used.
“If you add that per square metre, you use about 80% of the sun that comes in — and that's really good,” he says. With this method, you get heat energy from the PVT panels between 70 and 75 degrees Celsius.
“If you do the maths and have a good amount of sunlight, you can get about one kilowatt per square metre,” Van Someren says, “then, for every square metre of deck surface you use, you can generate 800 Watts of power.”
Custom conundrum: A conclusion
While the PVT panels for the sailboat are custom designed, one of the most important things the team realised during their building is how important it is to buy items that are readily available.
This means that rather than designing the panels from scratch, the team were able to save huge amounts of time and money in combining pre-existing components to make something new, rather than building it from the ground up.
It was this approach that enabled the custom PVT panels to meet the needs of the fossil-free sailboat, as well as being affordable enough to produce. This is a tough balance to strike in these instances.
Excitingly, these hybrid panels designed by the project team and its partners could have interesting applications for domestic purposes too, as they could be installed on buildings to harvest both electrical and thermal energy.
This is why innovation such as this one are vital. Making concentrated efficency gains in things like PVT panels not only benefits the maritime industry, but can also help make other structures greener and more sustainable. If we're going to enter a renewable future, we need to do it one step at a time.