The sailing yacht: hydro-generation, solar, electric and heat generation
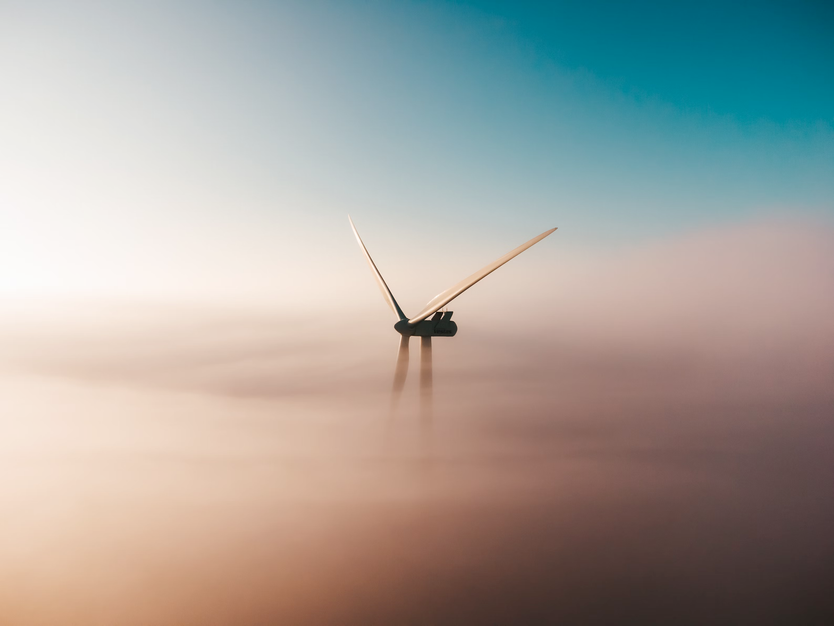
Foundation⁰ will develop knowledge and gather validation data to enable the creation of sailboats that are operated without fossil fuels on board.
The focus is on the development of technology to balance the energy production, storage and demand, without compromising on aesthetics and comfort.
This is accomplished through multi-disciplinary R&D, aiming at cross-pollination between different fields of expertise, with an open attitude towards possibilities and opportunities.
Foundation⁰ is all about developing knowledge and gathering data that will be shared on an open-source basis. A website is developed that will contain publications and raw data from experiments as these become available.
Research is currently still ongoing on each of the subjects shown in figure below and as this becomes available, the outcomes will be shared on foundationzero.org.
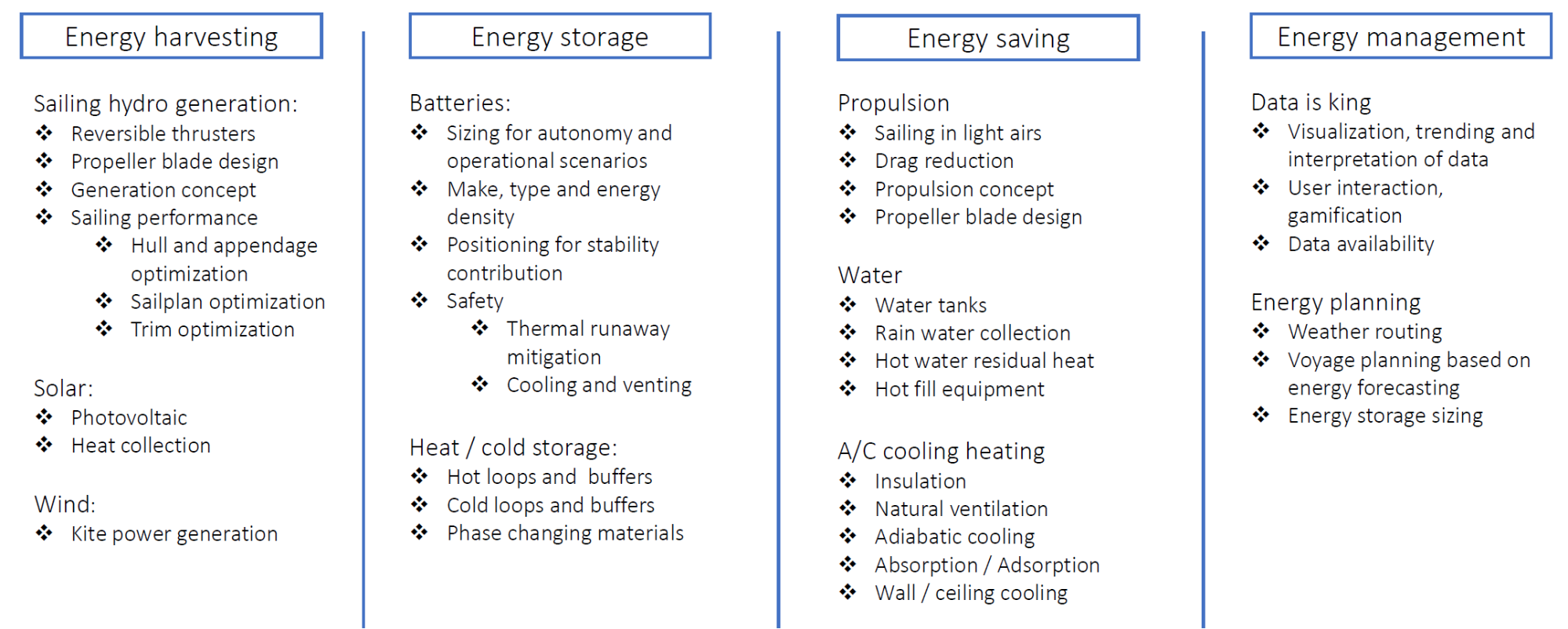
As an embodiment of the technology developed by Foundation⁰, a 69m sophisticated sailing sailboat is currently being built by Vitters Shipyards, with exterior and interior design by Vripack, naval architecture by Dykstra and contributions of countless sub-contractors and knowledge suppliers. The keel of this sailboat was laid in September 2022.
Energy Balance
To accomplish a fossil free sailboat concept, the energy that is used on board, needs to be produced on board. In the period between harvesting and consumption, it needs to be stored on board and this process needs to be carefully managed. In order to achieve an acceptable balance in the energy housekeeping within different operational scenarios, focus on each of these aspects is required. In the figure below, a typical energy balance for a conceivable operational scenario is shown. The graph shows the intention to run the hotel load on of the sailboat primarily on solar energy. The power required for propulsion, needs to be generated through sailing primarily. The State of Charge curve in this graph shows a net decline over the course of this week, requiring a net increase in the week after.

Today, we have identified the main contributors to the concept and will present two defining features that contribute to a fossil free sailing sailboat: “efficient hydro-generation” and “solar heat and cooling”.
Hydro-generation
The application of hydro-generation on board sailing sailboats is by no means new, but we see a steep increase in recent years. As a brief overview of the concept:
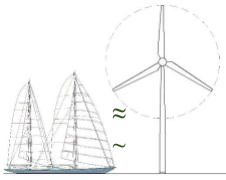
The amount of power that is involved in powering a sailing sailboat along is very substantial. For this panamax Ketch, the effective power of the sails in a fresh breeze, broad reach is in the order of 1.5 MW, roughly the same amount of power is generated by a common 70 m diameter modern wind turbine. This power is used to propel the vessel, i.e. it is converted to kinetic energy. To harvest some of this wind energy, and convert this to electric energy that can be used on board, a hydro-generator is used. In the case of a moving ship, a screw is the most likely candidate for this turbine. The hydro-generator converts the fluid’s kinetic energy into electricity by slowing down the fluid that flows through the turbine’s disk area . The maximum available amount of power in that flow is:
The hydro-generator in that disc can harvest a part of that power, limited by the turbine design and ultimately by the Betz limit. This ratio is expressed by the Rotor power coefficient (), where:
We found that for a 4-bladed screw, the maximum attainable is around 0.3 at a tip speed ratio around 3 (Advance ratio ). From the equation for and the limit found for , the conclusion is quite straightforward. In order to harvest a lot of power, the turbine disk area needs to be large and even more importantly, the flow speed needs to be high. So, for efficient hydro generation, a fast, powerful sailing sailboat is required with large hydro-generators.
In stationary applications of turbines, the drag that is associated with the retardation of the flow is relevant only for structural purposes. This drag does not affect the inflow speed. On a sailing vessel, the opposite holds true. The power yield of the turbine needs to be offset against the additional drag that it incurs since the speed loss due to this drag not only extends the duration of the trip, but it also reduces the inflow speed, cubically reducing the power yield. Therefore, in assessing the performance of the turbine, we have assessed the power coefficient against the prop efficiency. In the figure below this is shown for a Wageningen B 4-70 propeller. Work is currently performed at MARIN to analyze and optimize the propeller for hydro-generation.
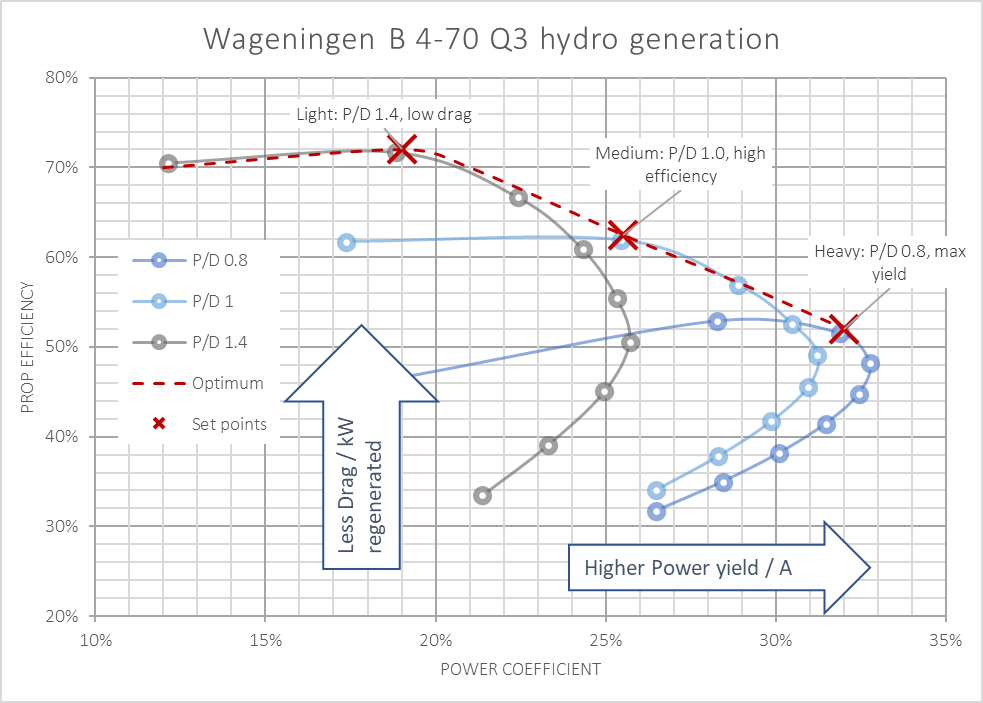
We found that to efficiently use a ship’s propeller as hydro generator, the orientation of the propeller blades would need to be changed between propulsion mode and generation mode to utilize the camber of the blades properly. This leads to a substantial increase in both power yield () and drag reduction, as shown below.
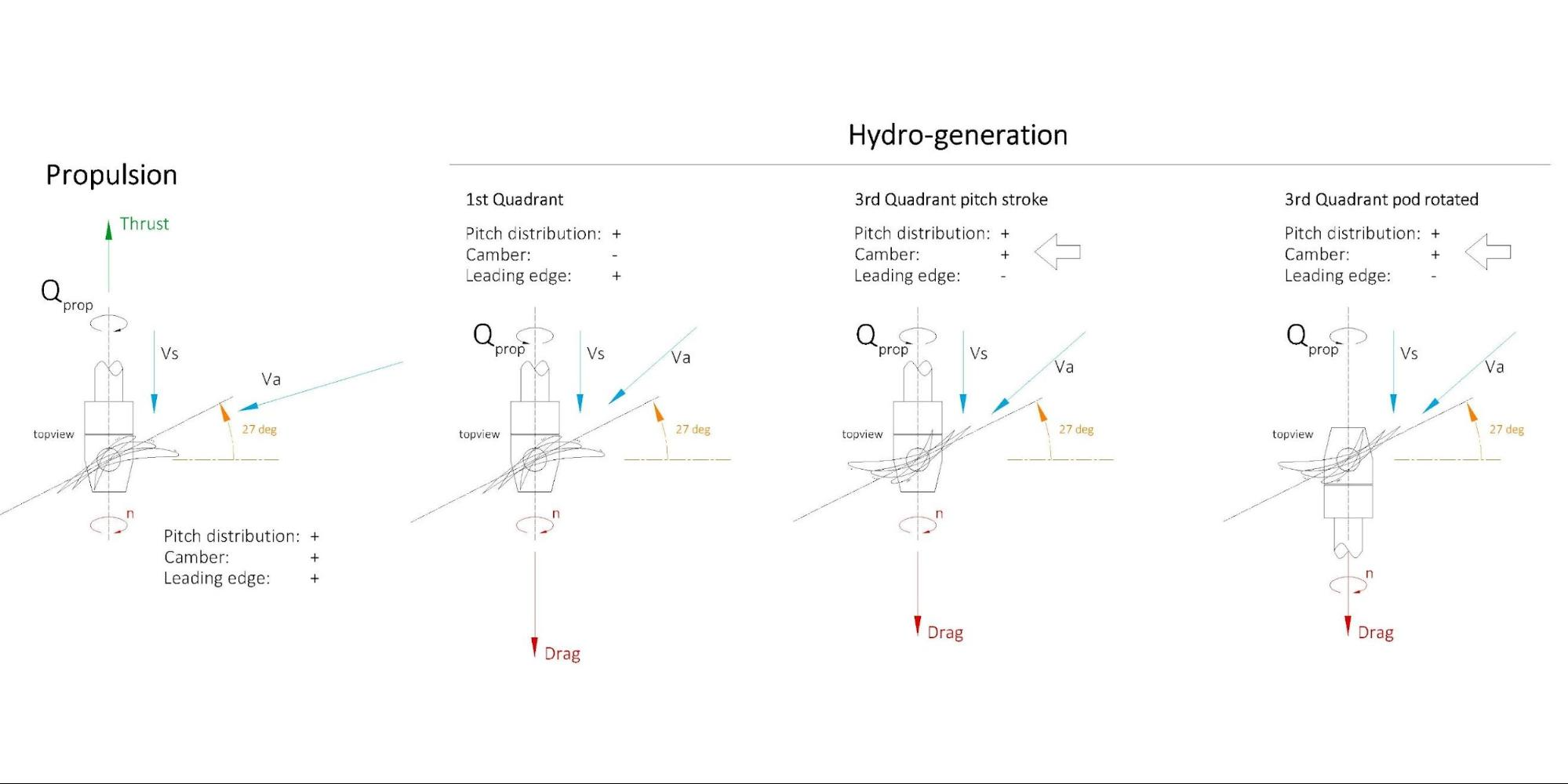
For this application, i.e. hydro-generation onboard a panamax ketch sailing sailboat, we have chosen a configuration with two azimuthing pods that can be used for propulsion, maneuvering and hydro-generation with a combined disk area of 2.9 m2, as shown below. The forward most thruster is optimized for generation while the aft thruster is optimized for propulsion. They can be used together in either mode.
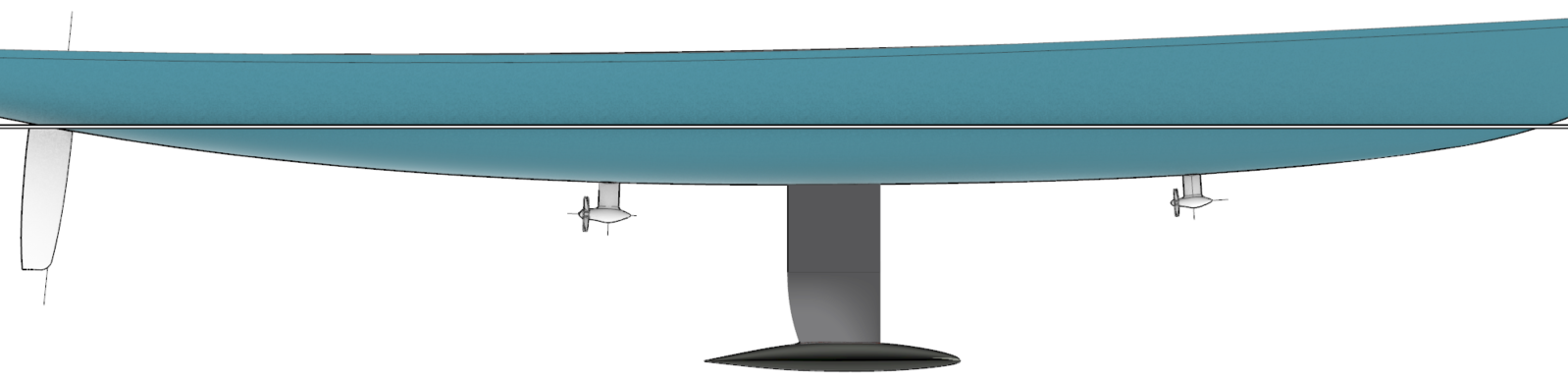
Once drag, from any source, is added to a sailing ship, the ship’s speed changes, altering the wind-triangle, sideforce production etc. Therefore, to do a proper assessment of the implications of using hydro-generation, the propeller in generation mode was modeled in a VPP environment. This led to new insights in the relation between speed loss and power yield, at different true wind speeds, for various pitch settings. Eventually this study provided guidelines for the maximum feasible prop diameter, based on the philosophy that only power can be harvested that exists, whilst balancing sail performance and hydro-generation capabilities.
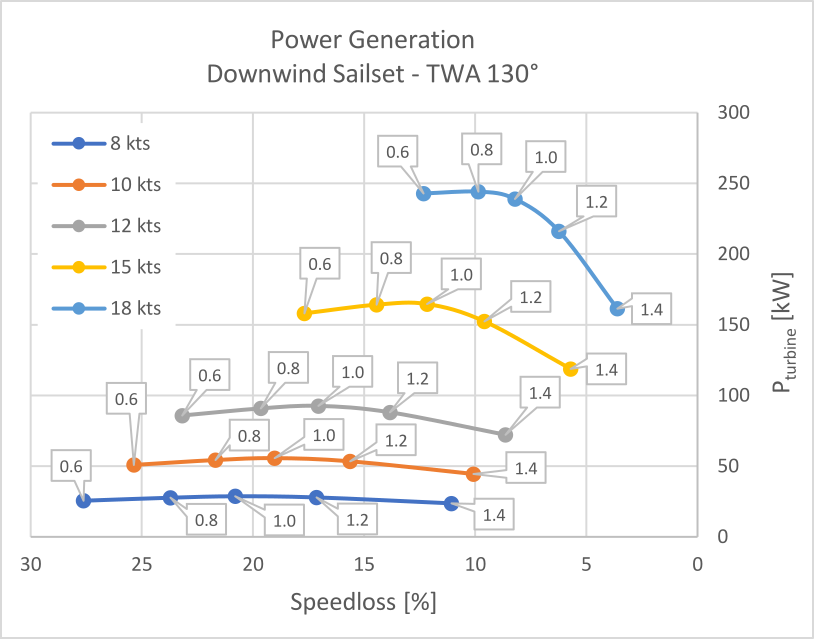
Solar Electric and Heat Generation
When the sailboat is anchored and there is little wind, sustainable energy harvesting relies on solar power alone. Apart from solar energy harvesting, aesthetics and safety play an import role and therefore the choice was made to cover only the Bimini and the cabin roofs with solar power collectors. Thus, we must harvest as much as possible of the incident solar power on those surfaces.
We have developed electronics to track the optimum power point for 8 to 10 PV cell layouts in the panels to mitigate the loss of output due to shadowing from the rigging. This approach increases the output by 10 to 20%, depending on the angle of the sun. Furthermore, the bespoke panels were developed to harvest not only Photo Voltaic (PV) but also thermal (T) energy from the same surface area. State of the art solar cells harvest approximately 20% of the solar energy as electrical power and the remaining 80% comes as waste heat as shown in the graph in the following figure.
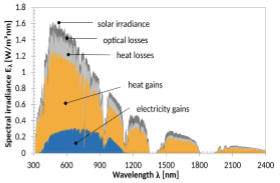
This heat is dissipated since with standard panels, it comes at a low temperature of ca 40 Celsius and is thus of limited use.
The design of these panels has a very high thermal insulation so that approximately 60% of the incident solar power is available as heat at temperatures of 80-85 Celsius. This high temperature makes the water heated in the panels usable for laundry, bathing and even for powering a 17 kW absorption chiller.
Typical domestic energy usage of a current day ship in this class is shown in the pie chart below. Not only can a significant portion of the power requirement be covered by thermal energy, in order to reduce the requirement, we are improving the thermal insulation of the deck and hull to reduce heat flow through those surfaces. This reduces the required cabin cooling capacity in warmer climates and in colder environments the cabin heating is reduced as well.
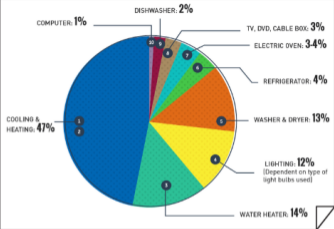
A significant gain in deck and hull insulation value can be made by application of ca 30 mm of cork over the metal plating of the deck. Furthermore, the use of an infrared reflecting additive to paint on the hull reduces the heat influx due to sun heating while not affecting the color scheme. The heat influx through the hull is hereby reduced by approximately 20-25%.
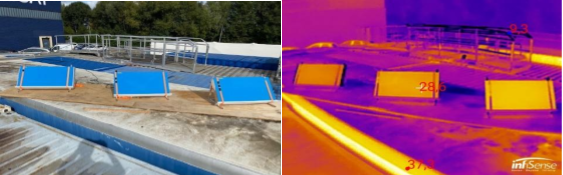
In the figure above, we see the visual image of paint test panels treated with (from left to right) IR reflective additive and insulating filler, only IR reflecting additive and the standard paint. Obviously, the IR reflective additive has no effect on the color. However, the thermal image or the right clearly shows the right panel is much brighter (thus warmer) and we measure a ca. 3.5 Celsius higher temperature. This is due to reduced heating of the left panel with respect to the right panel demonstrating the effect of reduced solar energy absorption due to the IR reflective additive and the insulating filler. Treating the hull with this solution reduces the cooling requirement of the ship, especially in the evenings when the sun is at a low angle.
This text was based on the white paper presented at the 27th International HISWA Symposium.